Green Highly Efficient And Economical Method Released For Recycling LCO And Ternary LIBs
| Jerry Huang
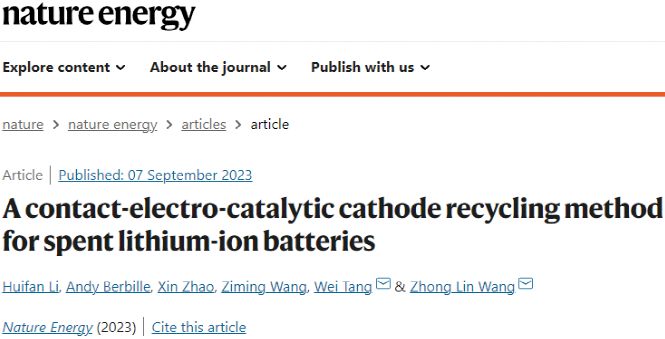
Editor's note: Lithium-ion batteries are now widely used in a variety of electronic devices, EV and grid-scale energy storage. Global demand for lithium-ion batteries continues to grow significantly. It is estimated that by 2030, the global volume of spent lithium-ion batteries will exceed 11 million tons, which will become a huge source of pollution that could seriously threaten the environment and public health. At the same time, the growing demand for lithium-ion batteries translates into a growing demand for lithium and cobalt. On the other hand, the content of lithium and cobalt in LIB cathodes is as high as 15% and 7% wt, respectively, which is much higher than that in ores and brines. Therefore, the recovery of metal elements in spent LIB cathodes is of great environmental, social and economic significance. Currently, the recovery of lithium-ion batteries is mainly divided into three steps: pretreatment, metal extraction and metal separation. In the research and development of the metal extraction step of the recycling process, the hydrometallurgical process is one of the most viable options because of its high metal leaching rate and satisfactory purity of the recovered products. However, the process is not so environment friendly, nor highly economical, because the use of inorganic acids brings hazardous by-products; while organic acids require additional reducing agents or longer reaction times and higher temperatures for metal recovery.
Researchers from Zhong Lin Wang team bring us a possible method that is green, highly efficient and economical for recycling LIBs, including lithium cobalt oxide batteries (LCO) and ternary lithium batteries.
Abstract
With the global trend towards carbon neutrality, the demand for lithium-ion batteries (LIBs) is continuously increasing. However, current recycling methods for spent LIBs need urgent improvement in terms of eco-friendliness, cost and efficiency. Here we propose a mechano-catalytic method, dubbed contact-electro-catalysis, utilizing radicals generated by contact electrification to promote the metal leaching under the ultrasonic wave. We also use SiO2 as a recyclable catalyst in the process. For lithium cobalt (III) oxide batteries, the leaching efficiency reached 100% for lithium and 92.19% for cobalt at 90 °C within 6 hours. For ternary lithium batteries, the leaching efficiencies of lithium, nickel, manganese and cobalt reached 94.56%, 96.62%, 96.54% and 98.39% at 70 °C, respectively, within 6 hours. We anticipate that this method can provide a green, high efficiency and economic approach for LIB recycling, meeting the exponentially growing demand for LIB productions.
Reference
https://doi.org/10.1038/s41560-023-01348-y